There’s something so satisfying about a well-formed piece of hand-thrown pottery. It might be the unique shape, the gentle sheen of its glaze, or the weight and feel, but once you’ve held a piece of handmade pottery in your hands, you will find it hard to go back to the millions of identical, mass-produced offerings.
The Tilehurst Pottery is a local business that creates beautiful, functional and unique pottery, and has done since 1999. Each piece is hand-formed and finished, possessing its own individual character and charm.
Recently, we spoke to Grant Pratt, who owns and runs the Tilehurst Pottery, to find out more about its history and what makes the pottery so special!
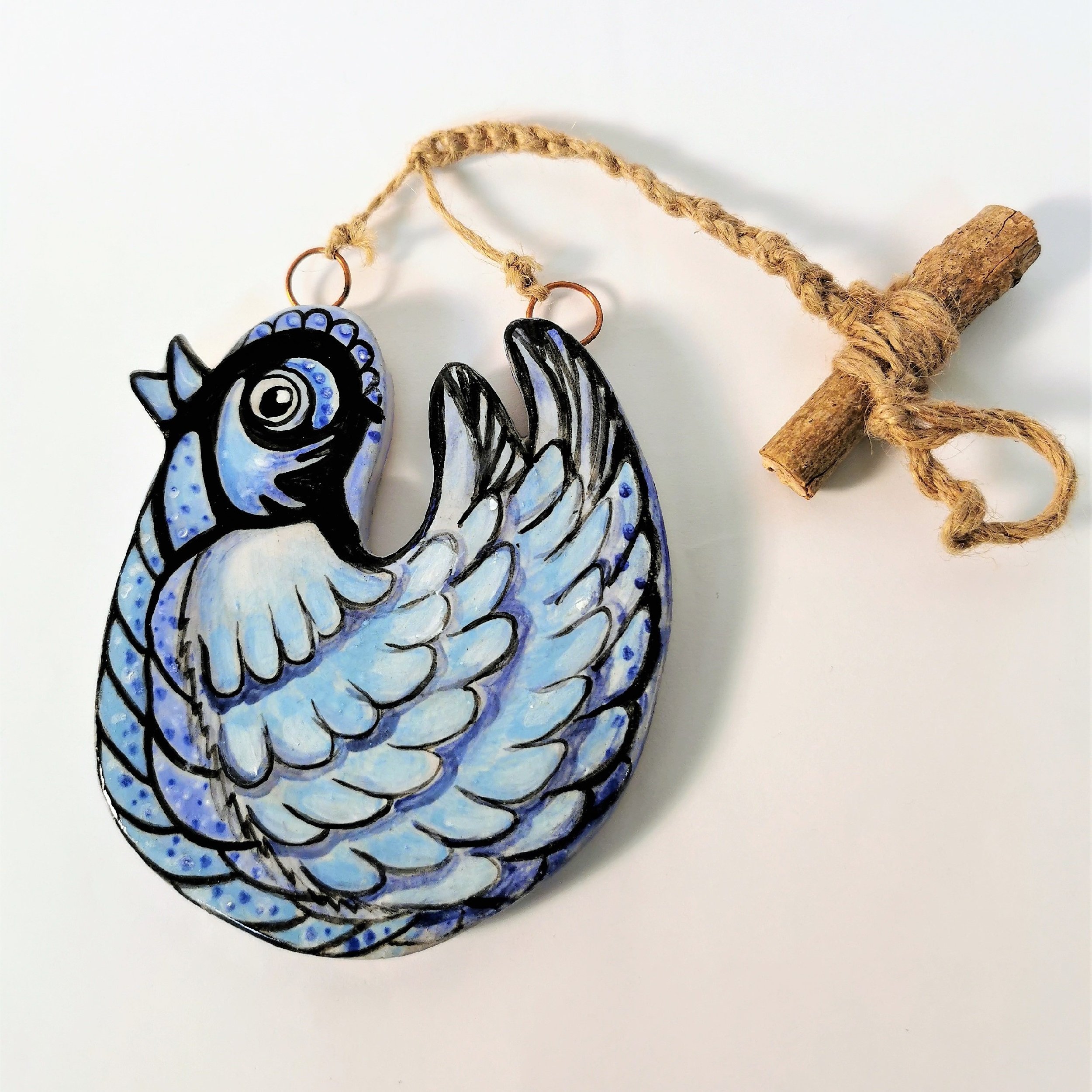
A hand-painted bird from Tilehurst Pottery!
Meet Grant
The Tilehurst Pottery is partnered with Bluematchbox, a Reading company that sells pottery supplies. We asked Grant about how the two businesses came to be.
'Bluematchbox had its beginnings in community art', Grant said, telling us that tile murals can still be seen at the MAPP Centre in Reading, Ranikhet Academy in Tilehurst, and High Close School in Wokingham.
'We’ve had fingers in many different pies over the years, but we’ve refined it down to the pottery and potters' supplies. The idea was that there’d be a perfect balance between the two businesses, but with the snowball of enthusiasm for pottery in recent years (in no small part thanks to The Great British Pottery Throwdown) the demand for supplies has boomed!’
The name of Tilehurst Pottery harks back to the tradition of craft pottery and artisanal production in Tilehurst, its namesake.
'I interpret the name Tilehurst as meaning village with clay’, Grant said. ‘It’s derived from Tigelhurst, with the word tigel meaning lots of different things, from clay to crocks to pots to tiles'.
Tilehurst’s history is interwoven with clay, and the place once teemed with industry manufacturing brick, tile, and flowerpots. 'The clay from the Reading beds stretches from Queensbury to Marlborough and possibly beyond', Grant said. Local people know about the brick and tile industry, but it took me reading it in a book to find out that Reading (and mostly Tilehurst) was massive in the flowerpot industry too'.
During the 19th century, two of the biggest producers in Tilehurst were the brickmakers S & E Collier Ltd and the tile and flowerpot specialists Tilehurst Potteries. 'My grandfather – not shy of a tall tale! – told me that, during the war, Tilehurst Potteries was turned into a sugar refinery and known locally as the treacle mines', Grant said. 'Then, in the late ’60s, Colliers closed. End of'.
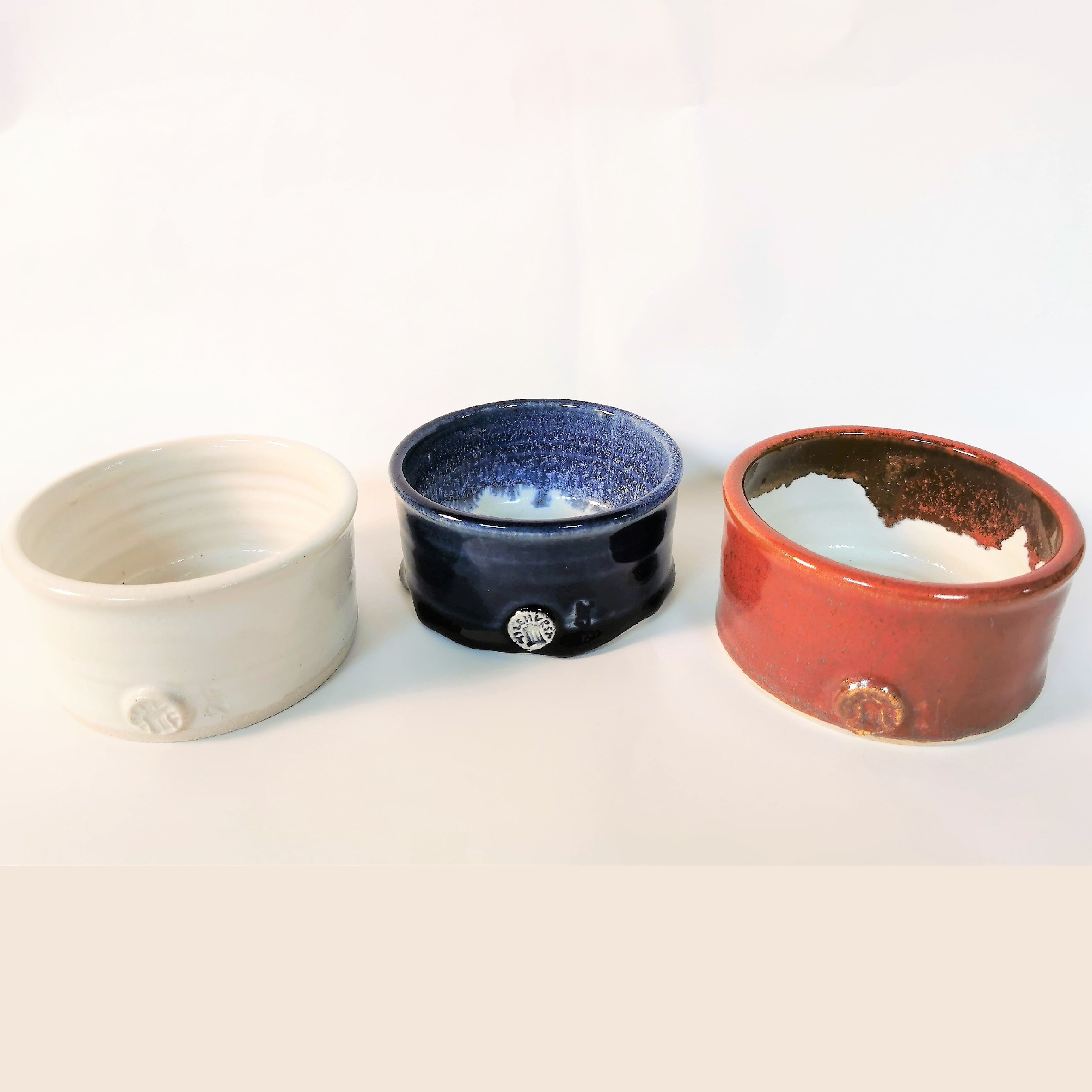
Three ramekins made by the Tilehurst Pottery!
A heritage of making
But this important heritage of making and craft wasn't lost forever. The high-quality, one-of-a-kind pieces crafted by the Tilehurst Pottery are a fitting legacy for the area’s rich industrial history. And in this way, Grant has become a custodian of sorts of pottery in Tilehurst. 'Although I have no direct connection, I am rooted or maybe steeped in the history of Tilehurst clay, unwittingly', Grant said.
We asked Grant about his process in making his pieces. 'All the work I do, apart from tiles, is on the potter’s wheel', Grant said. 'Clay is weighed out to suit whatever I am making, then it’s shaped on the potter’s wheel relatively quickly. It is then put aside to become ‘leather hard’: dry enough to handle without squishing it, but still wet enough to carve and add handles and spouts as necessary. After ‘turning’ and trimming it is again left to dry. It has to dry slowly and evenly to avoid cracking'.
When bone-dry, the piece is ready for its first firing, which is called‘Bisc firing. It is heated very slowly – no more than 100˚C per hour to around 1000˚C – otherwise it might crack or, worse, explode. 'Chemically-bonded moisture causes steam and can cause the pot to explode if too fast', Grant warned. 'Imagine a grenade going off in a safe – a bit like that'.
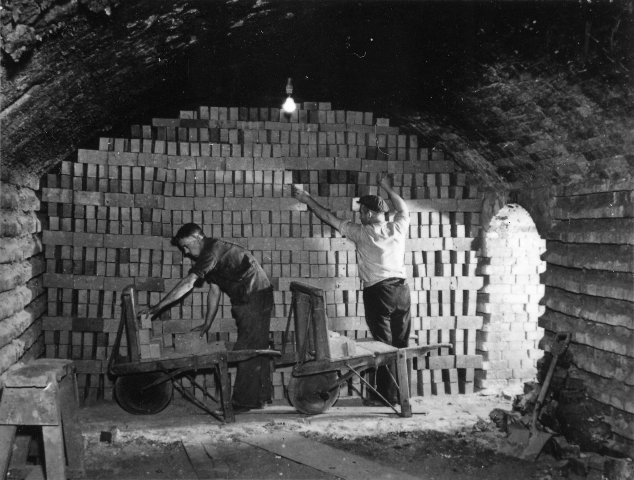
A brick kiln at Tilehurst, 1945. Museum object number REDMG : 1946.52.44
The art of decoration
Once a pot has been Bisc fired, it can be glazed or decorated. There are countless ways to do this, but the pieces produced by the Tilehurst Pottery are ‘dip’ glazed: dipped into a bucket of liquid glaze. The piece can then be fired to around 1280˚C so that the glazes melt. This higher temperature makes the piece suitable for ovens, dishwashers and microwaves.
In order to emphasise their individual character, the pieces are not overly finished. And this, Grant suggested, is the strong appeal of the Tilehurst Pottery’s hand thrown pots and vessels. 'Each piece is a unique creation controlled by hand and therefore shows off the vagaries of the human hand', Grant said.
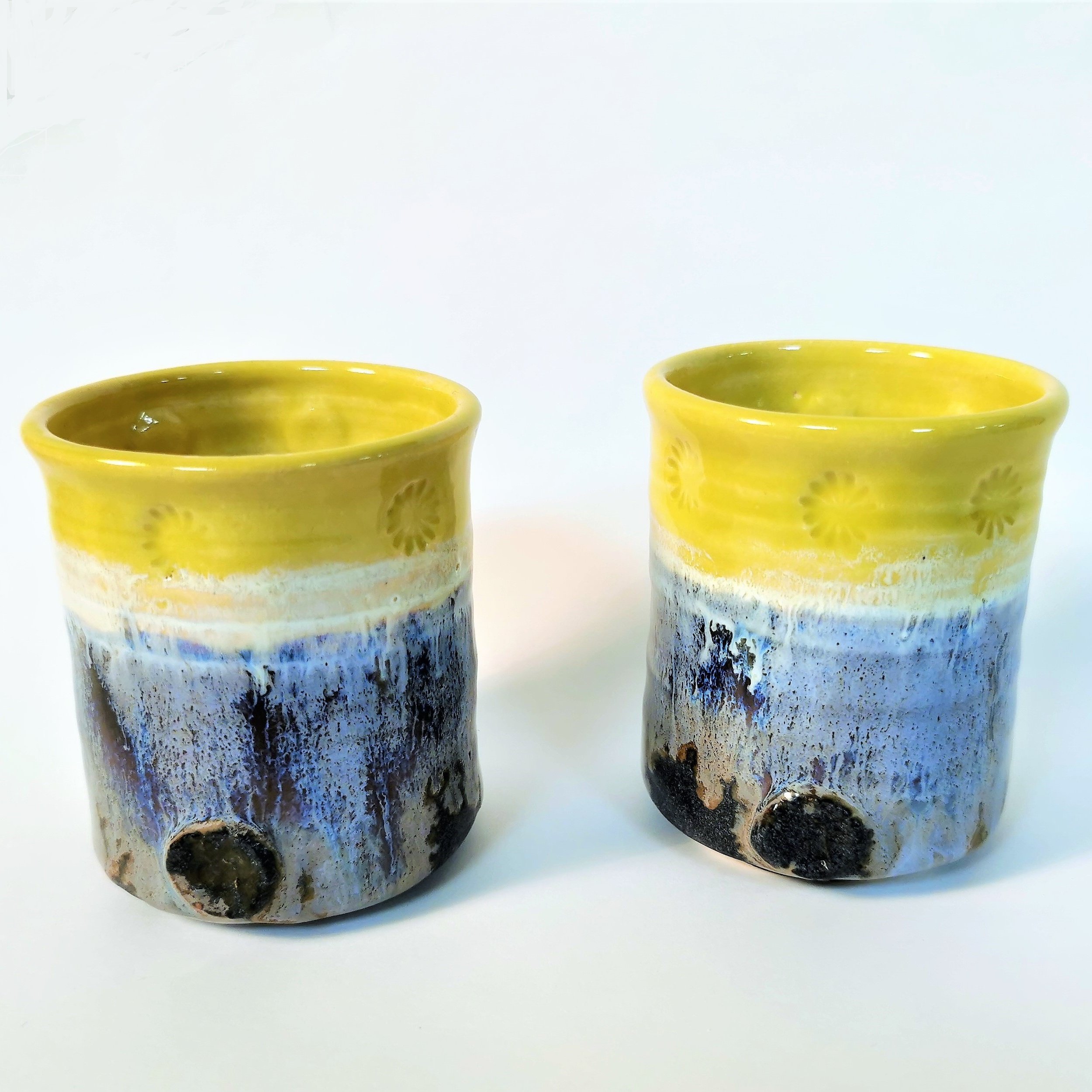
Two beakers made by the Tilehurst Pottery!
In our final question, we asked Grant for his favourite part of working at the Tilehurst Pottery. 'I need to make stuff', he replied. 'I think all humans need to make or grow or build stuff. Pelin – my wife – and I have taken a slightly ridiculous and bumpy path through life to try to carve out a creative existence. It’s the layers on layers and small steps that make working here satisfying. That, and being the boss!'
Our huge thank to Grant for taking the time to speak with us about life at the Tilehurst Pottery and how their beautiful pieces are made.
We are proud to stock a range of the Tilehurst Pottery's unique products in our museum gift shop, which reopened for customers to visit on the 12th April!
Visit the Reading Museum gift shop in person, or shop online using our new click and collect service.
Please note: products by the Tilehurst Pottery are only available to buy online through click and collect.